
As the Additive Manufacturing (AM) industry increasingly focuses on integrating technologies into manufacturing applications, the demand for automation across the entire end-to-end workflow is growing rapidly. With more 3D printers sold each year, the need for streamlined solutions—from advanced software tools to automation in the printing process itself—is becoming essential. Notably, the final step of post-processing must also evolve to enable labor-free finishing of parts.
To address this need, several companies are developing automated post-processing systems for removing support structures, finishing parts, and dyeing. These systems integrate software, hardware, and specialized chemicals to handle parts produced by various AM technologies.
One standout player in this field is AM Efficiency, a Swedish-based company dedicated to creating easy-to-use, mid-range post-processing solutions power-based AM technologies.
At Formnext 2024, I had the pleasure of meeting Casper Rosén, CEO, and Ulf Qviberg, CTO and Founder, to explore their innovative products and understand what sets them apart from competitors in the industry.

AM Efficiency booth at Formnext 2024. Image source: AM Efficiency.
How It All Began
AM Efficiency's journey started with a focus on reselling 3D printing solutions and providing services to the local market. This experience gave the company a deep understanding of the specific needs of customers, from choosing the right AM technologies to designing for additive manufacturing, exploring a variety of applications, and manually post-processing the parts.
Over time, it became clear that the market lacked suitable solutions for handling parts produced by SLS and MJF technologies. Two critical challenges emerged - Automation: streamlining labor-intensive post-processing steps, and Repeatability: ensuring consistent results with every part.
Additionally, the industry needed systems that were affordable and easy-to-use, particularly for mid-range powder-based AM systems.
The First Steps Toward Innovation
Leveraging their extensive experience and customer insights, AM Efficiency decided to address this gap by developing their own solutions. The team worked closely with end-users, ensuring their first product was designed to meet real-world needs. This collaborative approach not only refined the system’s functionality, but also ensured that the final product aligned with the specific demands of SLS and MJF post-processing.
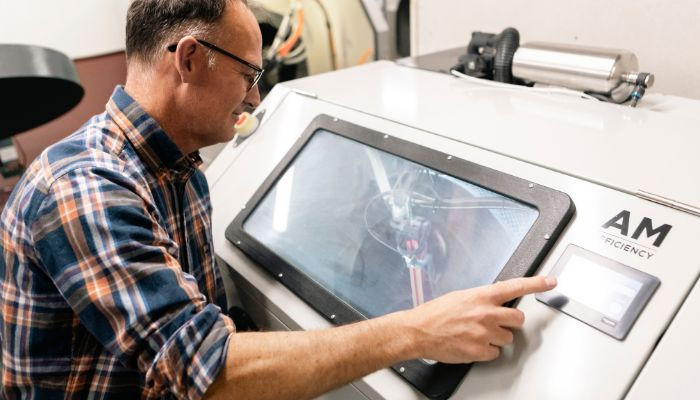
Casper Rosén, CEO. Image source: AM Efficiency.
Product Portfolio
AM Efficiency distinguishes itself by specializing exclusively in post-processing solutions for powder-based AM technologies. Their dedication to this niche allows them to address the unique needs of mid-range and high-end users with innovative solutions.
The company’s product lineup includes two key systems tailored to the specific demands of powder-based AM users:
CCP-10
Post-processing: cleaning, cleaning and coloring, or polishing
Suitable for SLS, MJF, or SAF technologies
Fast ROI – affordable cost
Cabinet volume: 440 liters
Drum size: Diameter 55cm, depth 30cm
Machine Size W x D x H: 1000x1100x1500
Weight: 170kg
CCP-20
Post-processing: cleaning, cleaning and coloring, or polishing
Suitable for SLS, MJF, or SAF technologies
Cabinet Volume: 990 liters
Drum Size: Diameter 850 mm, depth 400 mm
Drum Volume: 227 liters
Machine Size W x D x H: 1250 x 1250 x 1675 mm
Machine Weight: 210 kg

Automated mid-range post-processing solutions. Image source: AM Efficiency.
AM Efficiency at Formnext 2024
At the show, the company unveiled their latest innovation: the UNPIT. This groundbreaking product was developed in collaboration with Siemens, leveraging Siemens' expertise in automation and digitalization. What sets the UNPIT apart is its ability to automate the entire post-processing workflow, including:
Uncaking: Efficiently removing the powder cake surrounding the printed parts.
Depowdering: Thoroughly cleaning the parts to ensure all residual powder is removed.
Cleaning: Enhancing surface quality while maintaining precision.
Powder Recovery: Recycling unused powder for future use, reducing waste and material costs.
This fully automated solution minimizes labor involvement, boosts efficiency, and ensures repeatable high-quality results. Its modular design allows users to scale operations as needed, making it a valuable investment even for facilities with moderate part volumes.
The Benefits of the UNPIT System:
Higher Productivity: Automating multiple steps reduces processing time and labor costs.
Enhanced ROI: Even users with lower part volumes benefit from reduced waste and operational costs.
Sustainability: Powder recovery supports an eco-friendlier manufacturing process.
Seamless Integration: Siemens' digitalization tools ensure smooth integration into existing workflows.
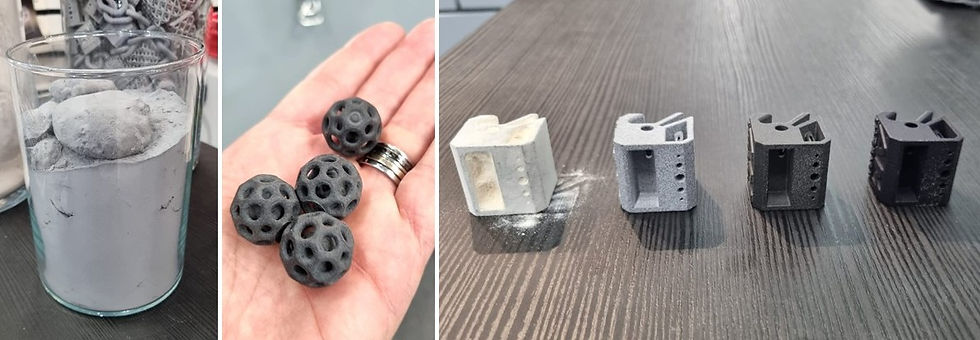
Fully automated 4-in-1 post-processing solution. Image source: 3D Alliances.
Automation is the Key
Powder-based additive manufacturing (AM) technologies are poised to play a transformative role in the adoption of industrial AM for manufacturing processes. As industries move toward scalable production, the demand for fully automated workflows becomes increasingly critical.
To unlock the full potential of AM, manufacturers will need to streamline every step of the process—from software design and printing to post-processing.
AM Efficiency's latest developments address these challenges by offering a fully automated, integrated 4-in-1 solution. This innovative approach not only reduces labor efforts but also eliminates ergonomic risks associated with manual handling, positioning AM Efficiency as a vital partner in the industrialization of AM for digital manufacturing.
Comments